Comprehensive Guide to Excavator Final Drives: Ensuring Power and Durability in Heavy Equipment
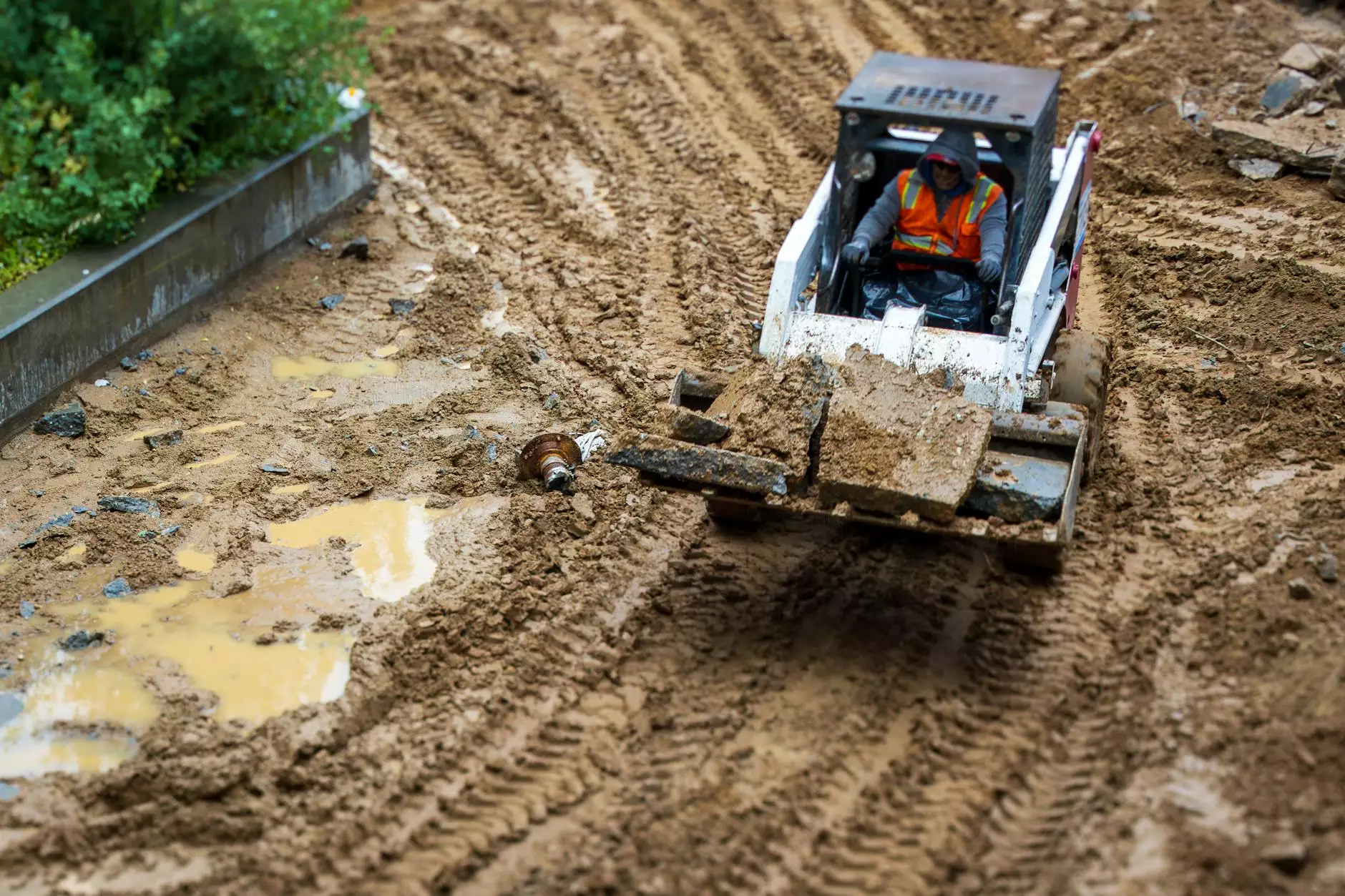
The excavator final drives are an often-overlooked but critical component in heavy construction machinery. These vital parts are responsible for transmitting power from the hydraulic system to the tracks or wheels, enabling precise control and movement on diverse terrains. Understanding the intricacies of excavator final drives can significantly enhance equipment performance, reduce downtime, and extend the lifespan of your machinery.
What Are Excavator Final Drives and Why Are They Essential?
An excavator final drive is a gearbox assembly that connects the hydraulic drive system to the tracks or wheels, allowing the machine to *move, turn, and perform excavation tasks*. It acts as the final gear stage in the power transfer chain, translating hydraulic energy into mechanical motion with high torque and efficiency.
These drives are subjected to demanding conditions—high loads, continuous operation, exposure to dirt, debris, and moisture—making their durability and reliability crucial for overall equipment performance.
The Functionality of Excavator Final Drives
The primary functions of excavator final drives include:
- Power Transmission: Convert hydraulic energy into rotational torque to drive tracks or wheels.
- Speed and Torque Adjustment: Allow smooth control over speed and torque, facilitating precise movement and stability.
- Durability Under Stress: Withstand harsh operational environments without failure.
An optimized final drive results in better traction, improved fuel efficiency, and safer operation, particularly in challenging construction sites.
Types of Excavator Final Drives
There are various types of final drives tailored to different excavator models and operational needs:
- Standard Final Drives: Used in most general-purpose excavators, robust but adaptable.
- Planetary Final Drives: Incorporate planetary gear systems for high torque at a compact size.
- Hydrostatic Final Drives: Utilize hydraulic fluid flow to power the drive, offering superior control in some models.
Choosing the right type depends on factors such as load capacity, operational environment, and specific application requirements.
Signs of Worn or Damaged Excavator Final Drives
Regular inspection and maintenance are key to preventing unexpected failures. The following are typical indicators that your excavator final drives may require service or replacement:
- Unusual Noise: Grinding, whining, or clicking sounds during operation.
- Reduced Mobility: Sluggish movements or difficulty turning.
- Excessive Vibration: Feelings of instability or rough operation.
- Leaks: Hydraulic fluid around the final drive casing.
- Overheating: Increased temperature during use, often linked to internal wear or lubrication issues.
Ignoring these signs can lead to more severe damage, costly repairs, and operational downtime.
Maintaining Your Excavator Final Drive for Optimal Performance
Proper maintenance extends the lifespan of excavator final drives and ensures consistent performance on your job sites. Key maintenance practices include:
- Regular Lubrication: Use the manufacturer-recommended lubricants to prevent internal wear.
- Routine Inspection: Check for leaks, unusual noises, and gear wear during scheduled maintenance.
- Maintain Proper Track Tension: Ensure tracks are neither too tight nor too loose to prevent undue stress.
- Keep Clean: Remove dirt, mud, and debris to reduce contamination and wear.
- Timely Replacement of Worn Parts: Replace gears, seals, and bearings at first signs of wear.
Replacing and Repairing Excavator Final Drives
When repair or replacement becomes necessary, choosing quality components is critical. You can opt for OEM (original equipment manufacturer) parts or high-quality aftermarket options, provided they meet or exceed original specifications.
Steps for Replacement:
- Diagnose the Issue: Confirm that the problem stems from the final drive.
- Secure the Equipment: Park on a stable surface and ensure the machine is properly supported.
- Remove the Old Final Drive: Detach connecting bolts and auxiliary components carefully.
- Install the New Final Drive: Align, secure, and test before resuming operations.
Professional installation and calibration are recommended to ensure safety and performance.
The Benefits of Using High-Quality Excavator Final Drives
Investing in high-quality final drives offers multiple advantages:
- Enhanced Durability: Superior materials resist wear and corrosion.
- Increased Efficiency: Better gear design results in smoother operation and lower fuel consumption.
- Extended Service Life: High-quality components last longer, reducing replacement frequency.
- Better Resale Value: Well-maintained, high-grade final drives improve equipment resale potential.
Choosing the Right Supplier for Excavator Final Drives
Reliable suppliers like shophydraulicamerica.com offer an extensive range of excavator final drives suitable for various brands and models. Key factors when selecting a supplier include:
- Product Quality: OEM or tested aftermarket parts with warranties.
- Pricing: Competitive rates without compromising quality.
- Customer Support: Technical assistance and guidance.
- Availability: Wide stock for quick turnaround and delivery.
Conclusion: Maximize Excavator Performance with Proper Final Drive Management
The excavator final drives are fundamental to the machine’s success, providing essential torque and mobility during demanding operations. Regular maintenance, timely repairs, and quality replacements ensure these components deliver optimal performance and durability. Investing in top-tier final drives and working with reputable suppliers like shophydraulicamerica.com can significantly reduce operational costs and enhance productivity.
Whether you operate a small construction outfit or a large industrial fleet, understanding and prioritizing the health of your excavator final drives is vital. A well-maintained final drive translates to smoother operations, lower downtime, and maximum return on investment.
Additional Resources for Heavy Machinery Owners
- Operators’ Manuals: Always follow manufacturer guidelines for maintenance and troubleshooting.
- Professional Servicing: Schedule periodic inspections with qualified technicians.
- High-Quality Replacement Parts: Choose trusted brands and suppliers to ensure reliability.
- Training and Education: Equip your team with knowledge on proper machinery handling and maintenance best practices.
By staying informed and proactive about excavator final drives, you secure your machinery’s performance, safety, and longevity—fundamental elements for success in the heavy equipment industry.